This is a more refined version of the plough discussed in an earlier post. I’m not sure it is all that desirable to have a “convertible” plough but this was an interesting experiment for me. In fact the larger version can easily be used to trim thin books. The tool is a little heavier but I’m not sure that is a significant drawback.
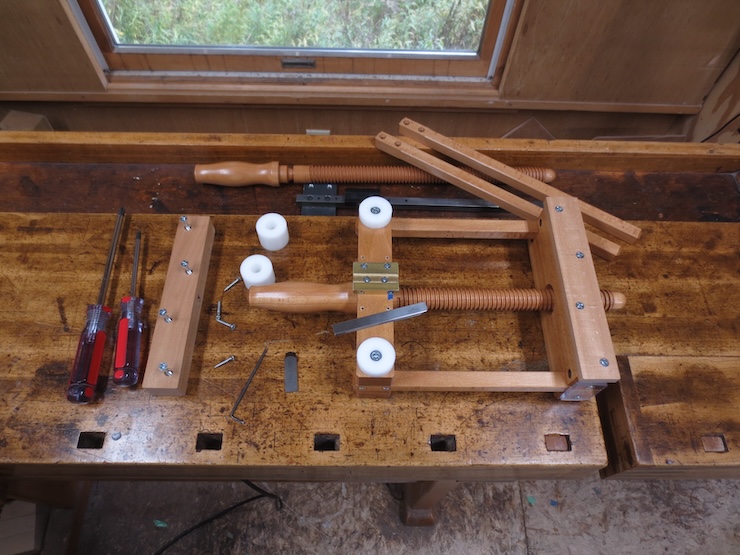
Laid out on the bench are all of the parts needed for this plough in either configuration. The plough is designed to work like a traditional bookbinding plow with a trimming capacity of about 2-1/2″. By substituting a set of parts it can be converted into a plough with a very wide cutting capacity of over 4″.
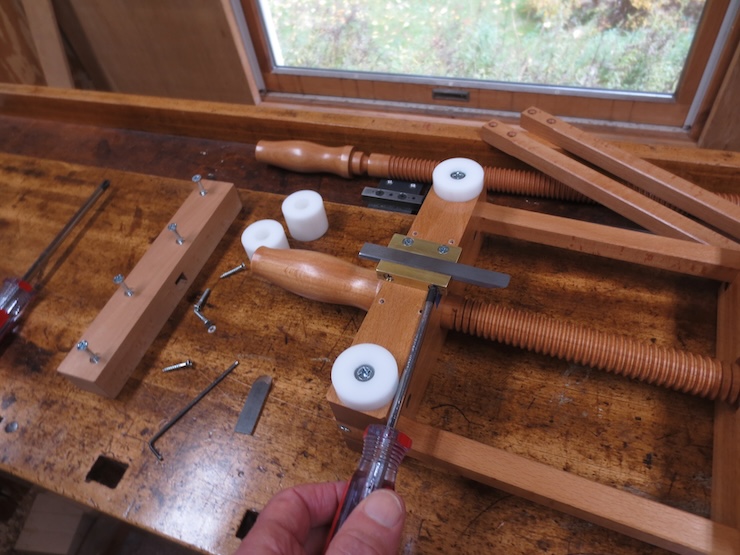
In the conventional mode the dovetail knife is clamped into a machined brass fixture. It can be set for different widths of cut by loosening two screws. Very gentle tightening holds the knife firmly in place. The knife is 1/8″ thick, a little more than 1/2″ wide and 4″ long.
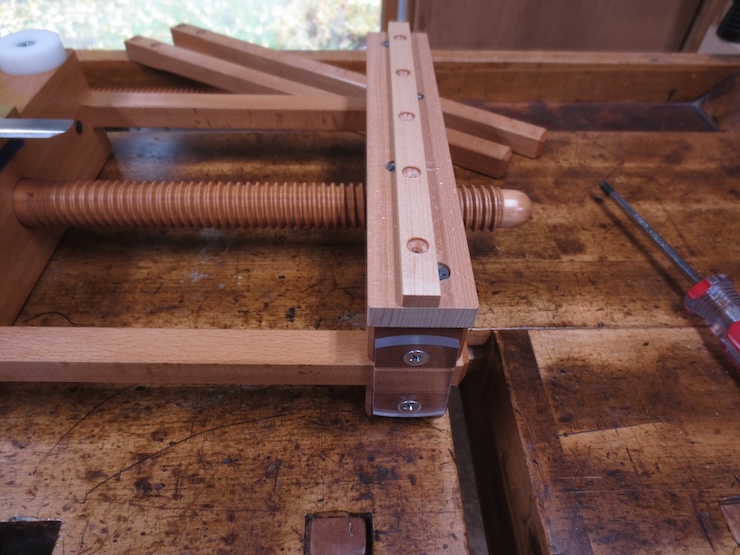
Presses vary in how the tracking side of the plough fits. This plough doesn’t have a tracking strip yet but it might look like the one shown here.
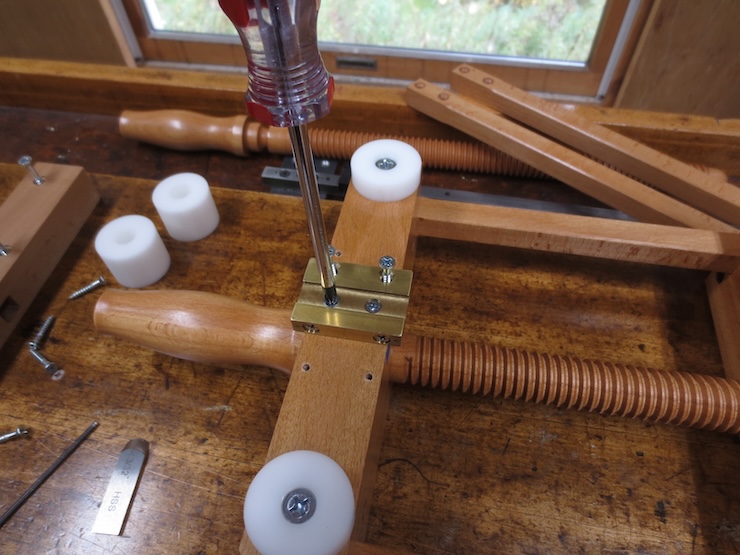
I will convert the plough from the traditional mode to the more experimental version. The first step is to loosen screws to remove various parts.

The blue tape is a shim that tilts the point of the knife down just a bit so the body of the knife won’t rub on the freshly trimmed pages.

These slide discs are sized to lift the knife side of the plow enough that the knife clears the press. These are removed since the new arrangement will require thicker discs.

The steel pin that retains the wooden screw is pushed out.

The screw is backed out of the threaded part of the plough and removed.

Now the two guide bars are removed.
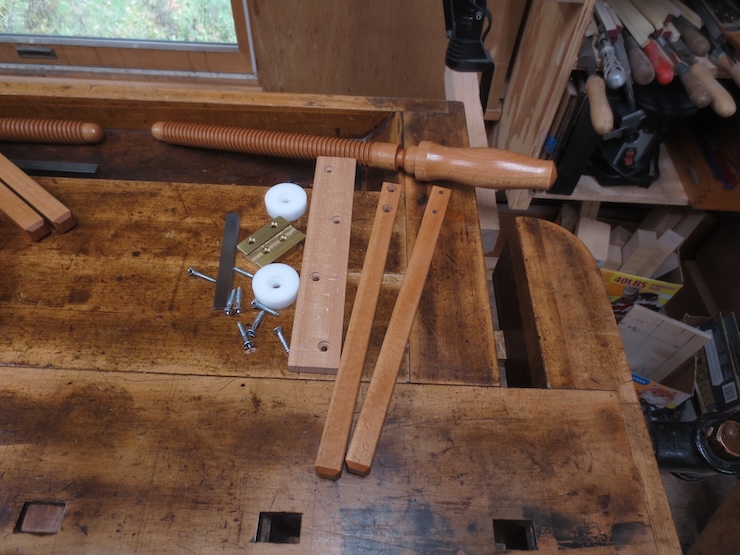
Here are all the parts that have been removed.
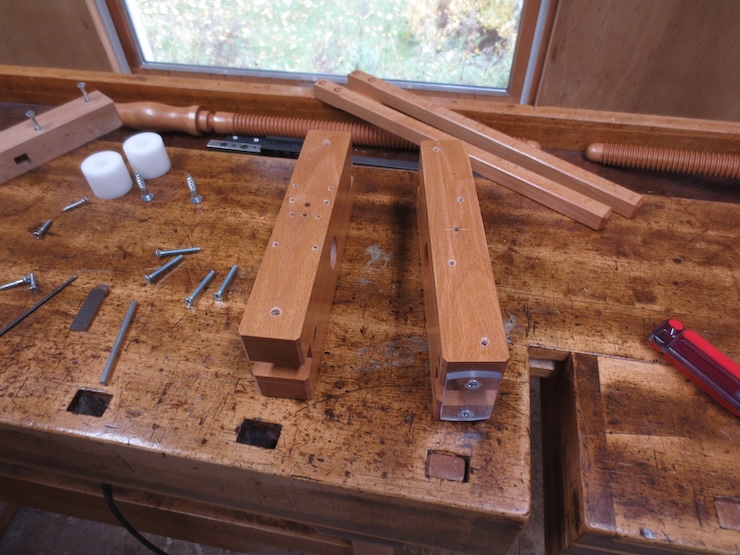
The two parts of the plough body are ready to receive the alternate parts.
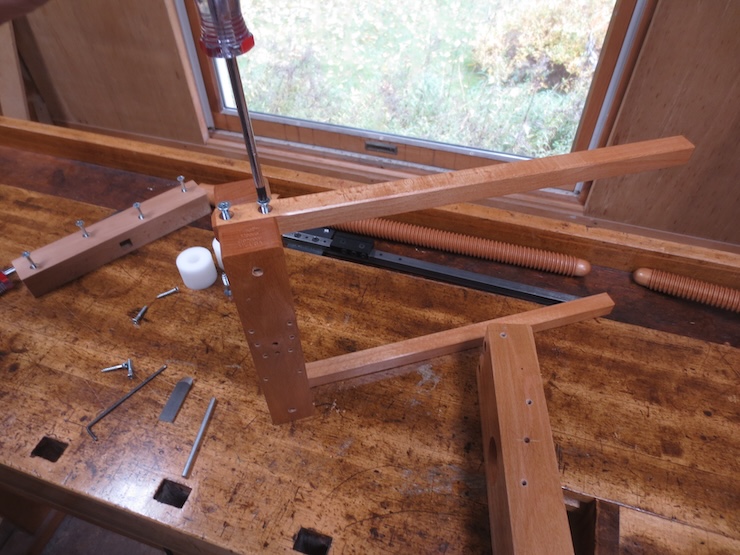
Longer guide bars are installed.
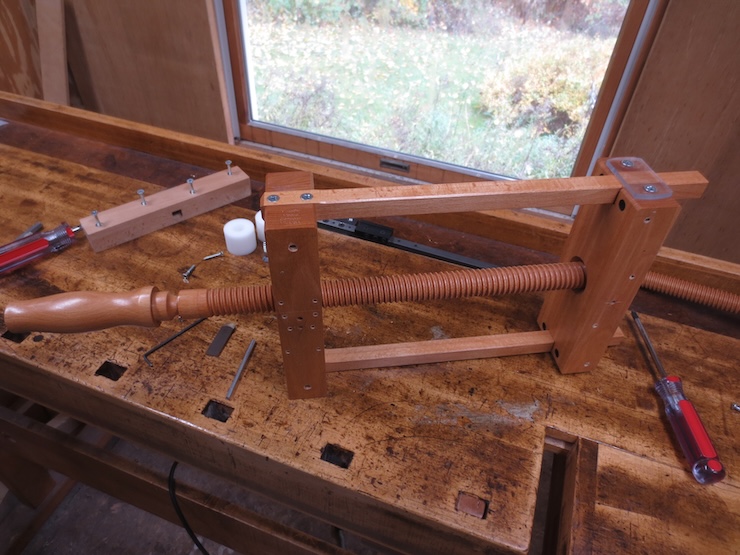
A longer wooden screw is threaded into place.
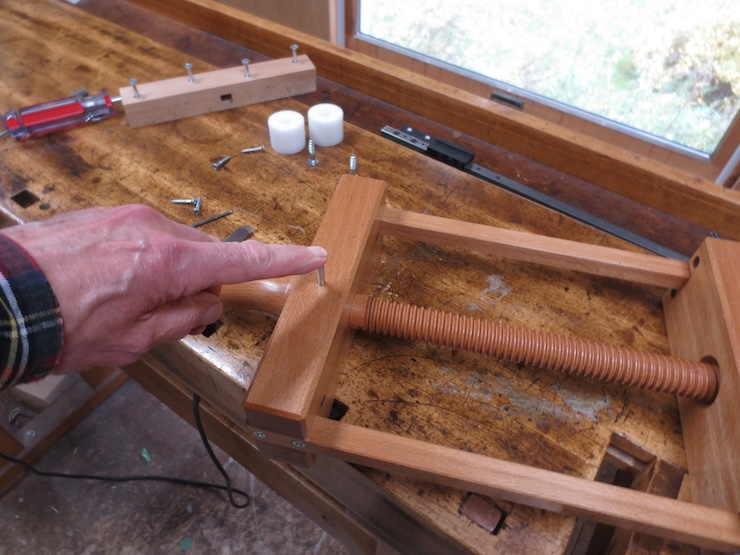
The steel retaining pin is re-inserted.

The long screw is now locked into the plough but free to turn.
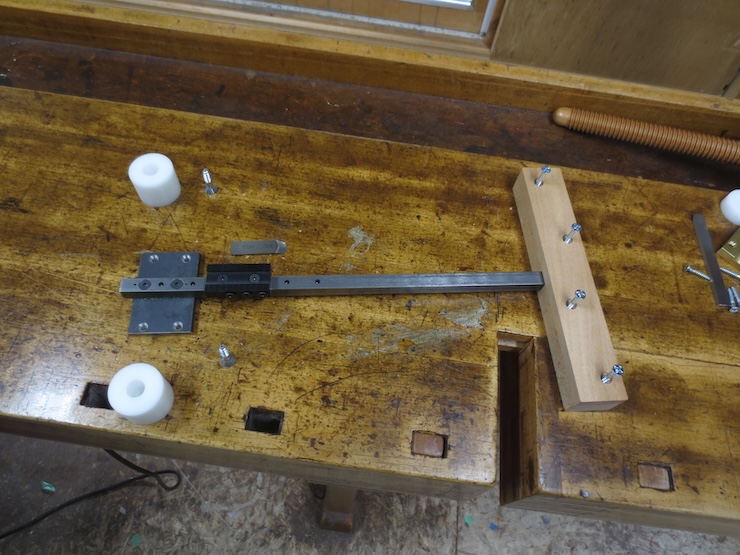
These parts will now be added.
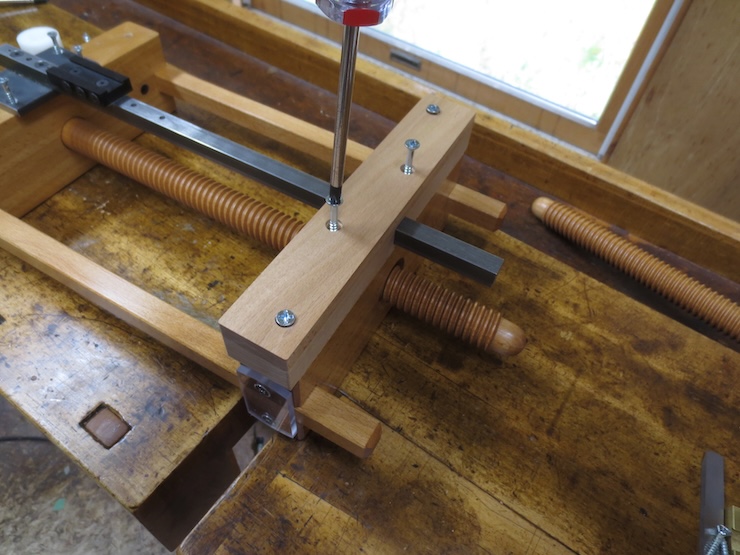
The block on the tracking side is made of two layers with a carefully fitted notch for the steel bar to slide in.

As before this shows what the next step might be to fit this plough to a tracking groove in its press.

The other end of the bar is fastened to the handle side of the plough with four screws. The thicker slide discs have been secured with the same two screws that were used for the thinner ones.
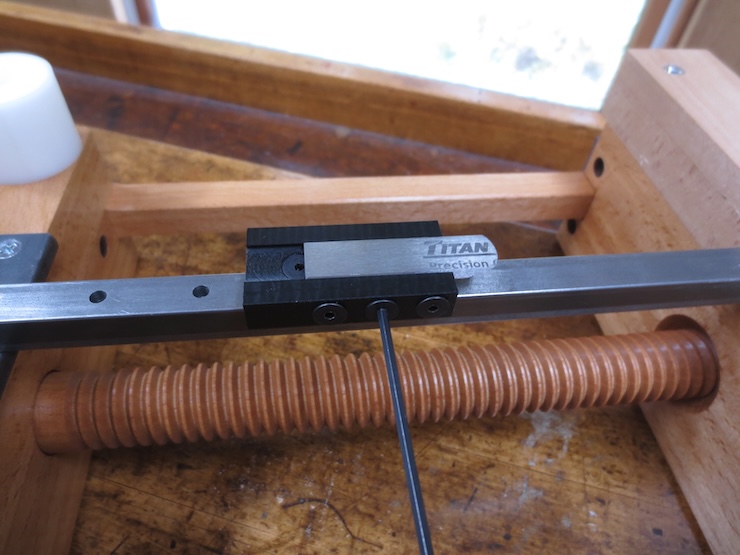
These clamping screws are tightened with a hex wrench. Very little pressure is needed to secure the knife. This dovetail knife is smaller at 3/32″ thick and about 2″ long. It is a little easier to make because there is less metal to grind away. Both sizes of knife are re-ground from high speed steel (HSS) jointer knives. (A jointer is a woodworking machine.)

The knife clamping fixture is machined from acetal plastic. It is about 2″ long and can be positioned in five different locations along the bar with a pair of screws. These are also tightened with a hex wrench, but firmly. A small piece of masking tape lowers the point of the knife a little so the rest of the knife doesn’t rub.
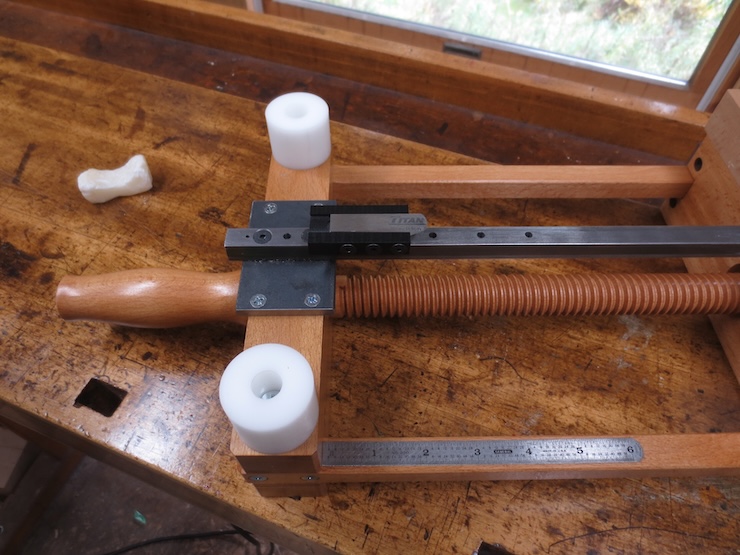
Here the knife is set to cut about two inches of book width.
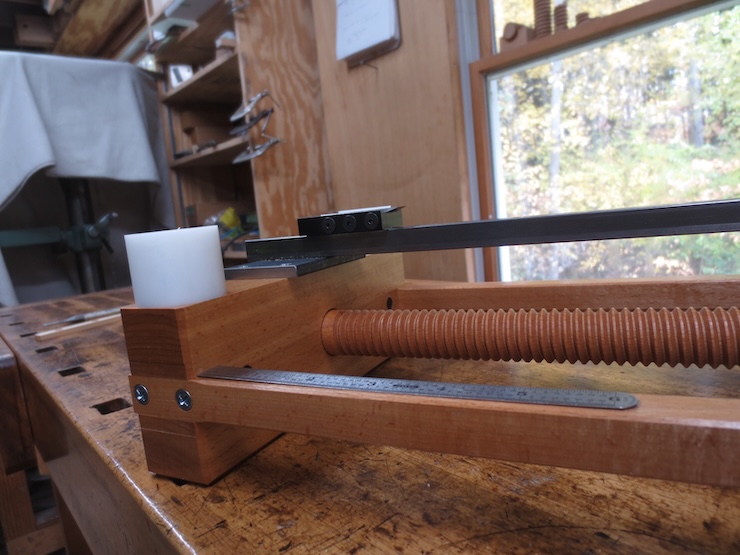
This shows the knife in relation to the slide discs. When the plough is right side up the tip of the knife will be about 1/16″ above the press. The knife holder can easily be shimmed down if a closer setting is preferred.

The complete plough from the bottom.
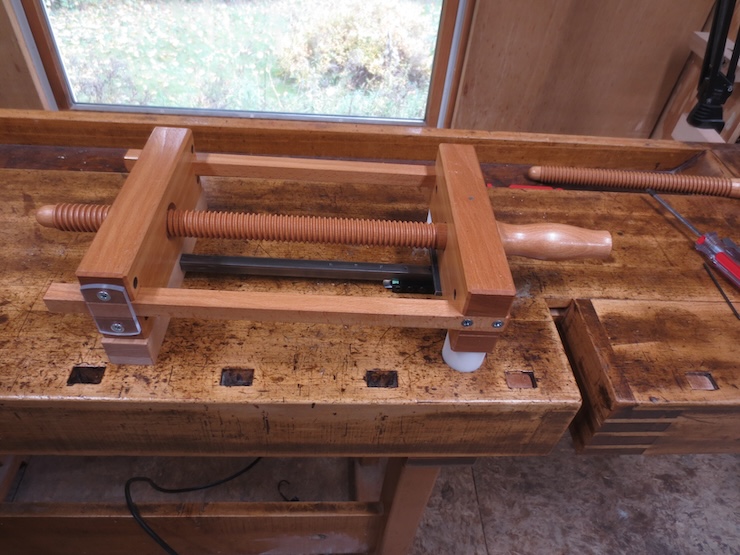
The plough seen from the top. I am not a bookbinder but I have used the plow in both forms. I believe that it works very well.
As I understand this increased knife reach the intent is to cut across ganged books. This is similar to ganged edge gilding, If so other fixtures are needed including Germanic saddle rests to align the ganged books.
LikeLike
I am familiar with the concept of trimming ganged books with a plough but can’t claim that this was my motivation. I think I am just intrigued with the functions of tools in general and if they are fairly simple (seemingly) it is a challenge to try to improve or adapt to available materials etc. Often the ‘simple’ tool turns out to be more complex than originally thought.
LikeLike